Ball Hone Grit For Cast Rings
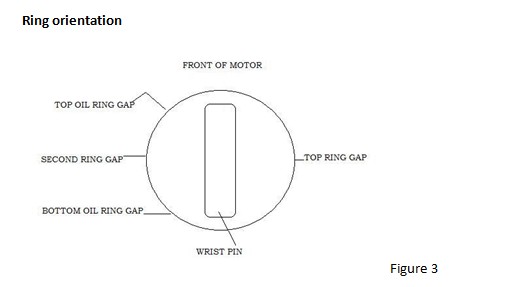
For moly rings a two step honing process can be used to achieve a plateau finish.
Ball hone grit for cast rings. Our guidelines are as follows. I will be running forged pistons. The ball hone tool is great if you are only trying to freshen a cylinder prior to re ringing. These hones are self centering self aligning and self compensating for wear unbreakable honing device with long life and consistant finish made in u s a.
Also lots of honing oil and 8 to 12 strokes per cylinder and a good cleaning afterwards then you are good to go. Ball hones provide a great surface finish and will make your next re ring job a success. I remember that back in the day the machine shop had to hone the block different for moly faced rings vs cast iron rings. 320 or 400 grit.
Using to fine of a grit will not allow you to properly lap the rings in and using to coarse of a grit will wear your rings quickly. Most of the time i have ran moly rings. Substantial controversy exists on the correct cylinder roughness for proper seating of piston rings whether chrome moly or plain cast iron. Forums all over the web debate what solution will provide the proper finish for seating piston rings.
The flex hone is a fast and effective solution that any hobbyist can do themselves. It has been our experience that the use of 220 280 grit stones and achieving proper cross hatch angle produces a finish compatible to all three types of the above rings. 180 or 240 grit. This hone is for a 4 4 125 inch bore and has a 120 grit.
If this is going to be a re ring then we recommend the 120 grit silicon carbide flex hone bg 350 for cast rings in high nickel blocks and the 320 grit bg 350320 silicon carbide for moly rings. First hone with a conventional 280 grit silicon carbide vitrified abrasive. Iron cylinder ring type. So what honing stone or grit should i ask for i get the block bored.
A very common diy application for the flex hone is deglazing cylinder walls to prepare them for new piston rings. 240 or 320 grit. Our best seller to commercial engine rebuilders and power sports shops is the 240 grit hone. Then finish by briefly touching the bores with a 400 grit stone or giving them several strokes with an abrasive nylon honing tool or brush.
320 or 400 grit. Choosing the incorrect hone grit whether to course or too fine can cause multiple problems that lead to poor engine performance or failure. This is for honing a block for cast rings. Ball hone how to get the perfect finish for piston ring sealing the ball hone is self centering self aligning to the bore and self compensating for wear.